Weight Lines, Snatchblocks, and Flight Paths
© Donn Haven Lathrop 1996
Shelf clocks and tower clocks both use gravity drive systems to drive
their works and thereby indicate the time of day, whether it's with 2
.5 inch hands and a strike on a 1 ounce wire gong, or with 6 foot hands
and a strike on a two ton bell.
Massive tower clock weight systems have been in use at least since Henri
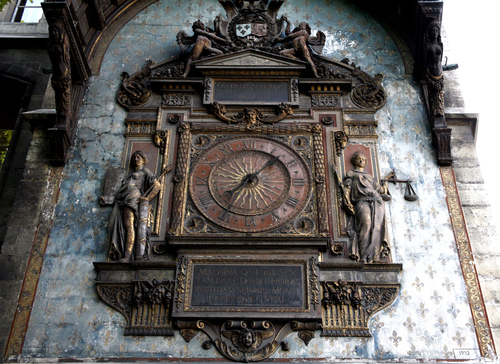
Figure 1. The Dial of Henri de Vick's 1370 clock.
de Vick installed his 1370 tower clock in the Palais du Roi in Paris
with a 500 pound weight for each train, but there is little to nothing
in the literature on the subject of weights, weight lines, and their
auxiliaries--particularly those used in tower clocks.
More and more old
tower clocks in this country are being restored to their original
weight drives, or updated with new weight lines and pulleys, therefore
the possibility of serious error in the installation, handling, and care
of these weight systems becomes very real.
Error can become tragedy if carelessness or inadvertent ignorance
damages a century-old tower clock, or the building in which that clock
measures the minutes of its second century.
Many of these buildings--churches, town halls, academies, grange halls, and mills,
are now on the National Historic Register.
They are a part of our
heritage--we cannot afford to be careless with them, because
carelessness can precipitate the destruction of a building through
well-meaning, but ill-informed, cleaning and maintenance procedures1,
and carelessness can cause injury or death if an errant weight plunges
through a ceiling into a sanctuary, office, or entryway.
Granted that insurance can take care of building repairs and medical costs, but very
few insurance companies today are in the resurrection business.
For a novel, known-to-work "catch" or "weight stop" method, go to:
[intended reference unknown /ed.]
1 The custodian
of a New Hampshire church once enthusiastically suggested the use of a
bucket of gasoline in the clock room to clean the transmission and the
motion works.
I'm afraid my reply was not couched in words suited to a house of worship.
1
Although the focus of this article is
primarily on tower (public, steeple, or turret) clocks, much of the
information, on a considerably reduced scale, can easily be applied to
the smaller clocks most of us work with on a regular basis.
There is no danger in a kinked weight line or a broken weight pulley in a tall-case
clock, or in the three pound weight of an O.G. falling to the bottom of
its case, (other than a heart attack when it hits bottom)2
but there is very real danger, to both people and property, in analogous
situations involving tower clocks and their weight drive systems.
A note published in 'TOWER TALK', the newsletter of NAWCC Tower Clock
Chapter 134, attests to the Occupational Safety and Health
Administrations (OSHA) display of a very real interest in the potential
dangers posed by the great weights of both pendulum bobs and driving
weights, as well as other potentially injurious characteristics of tower
clocks.
OSHA is checking on the installation and maintenance of clock
cables (hereinafter referred to as weight lines), the ratchets on great
wheels, as well as ladders, stairways, trap doors, and any other booby
traps in which the well-meaning but vulnerable clock custodian and
others can get caught.
As a clockmaker, you are not concerned with the
construction of ladders and stairways, except as they affect your
ability to reach the clock safely.
But, if you work on the clock, the
weight lines and the weights, it is very much to your advantage, not to
mention the clock owner's benefit, to do the work right, and to do it safely.
It is a good idea to become familiar with the OSHA
requirements for stairs and ladders, and to (tactfully) point out any
deficiencies to owners of tower clocks, simply because OSHA will, sooner
or later, inspect all tower clock installations, and if access to the
clock does not meet those requirements, the clock may well be shut down
until the deficiencies are corrected.
I might add that there is no grandfathering--it's either fix it or shut it down.
2 I recall an
O.O.G. sitting on my wife's piano when a weight line broke.
When I came down off the ceiling, I would have sworn that a string for low C had
snapped, or that the soundboard had cracked.
2
Terminology:
Tower clock gravity, or weight, drive systems need: (1) a common
terminology and nomenclature, simply because most horological handbooks
and dictionaries give short shrift to even the simple weight systems
used in house clocks; (2) definitions for some of the equipment and
accessories specific to tower clocks and tower clock weights; and (3)
some information on installation, safety, and maintenance considerations
for tower clock weight drive components.
Weight systems have been
around for so many centuries that it is apparently assumed that everyone
knows everything necessary, and that the terminologies and practices
applicable to household clocks are adequate.
The lack of installation
information is nearly total, and on safety and maintenance there is no
information at all.
Learning how to replace and maintain tower clock
weight drive systems via the school-of-hard-knocks method is fraught
with many dangers; dangers to the clock and the building in which it is
placed, to yourself, and to the people who use the building.
|
Safety is the primary, and the only, consideration
in any work on a tower clock weight system.
|
If you can get the clock running without encountering, or creating, any
sort of an unsafe situation, well and good. If not, the best procedure
is to correct the unsafe situation first, whether you do it yourself,
or whether the clock owner has someone come in and make repairs. It's a
real thrill to bring one of these old clocks back to life, but, don't
endanger the life of anything else--a building, the clock itself, or of
any person in the vicinity of the clock. John Stutsman mentioned in his
"Clockmaker's Corner" in a recent issue of the (NAWCC) BULLETIN, that
state governments had given up on trying to set up and impose licensing
requirements for clock repairers. Therefore, before you become a 'fool
rushing in where professionals fear to tread', stop and think and plan
and ask questions--in other words, license yourself. I would rather not
have a bureaucrat looking over my shoulder every time I restore or
re-oil a tower clock.
3
I've seen and repaired the handiwork of too many incompetents on too
many tower clocks, much less household clocks. The ability to work on a
tallcase clock does not qualify you to do similar work on a tower
clock. Someone's life may literally be in your hands; please be
careful.
Modern nomenclature of various accessories and mechanical
contrivances used in hoisting and wire rope systems will be defined in
appropriate sections in this article, and in the appended Glossary.
Nomenclature with which we are already familiar will be used as much
as possible to avoid the confusion of multiple terms which refer to the
same object. New terminology will be proposed, and its use justified.
Mathematical formulas and tables will be found in the appropriate
appendices.
Weight Line Definitions and Nomenclature:
The literature is filled with references to systems with two lines at
the weight referred to as doubly compounded, and systems with three
lines at the weight referred to as triply compounded--on the other hand,
within the pages of a single reference, I found identical weight
systems referred to as "compounded once"; later, double compound:
another referred to as "compounded twice"; later, triple compound. This
lack of any kind of specific definition is confusing, and confusion
isn't needed when you're going to be working in mid-air, so to speak,
with 800 pounds of strike weight. Since a simple compound system
already has two lines at the weight, double compound suggests four lines
at the weight, and triple compound suggests anywhere from six to nine.
The clockmaker working with tower clocks also needs to be able to
'speak the language' of the rigger and the crane operator, because these
professionals daily deal with all of the components that make up the
tower clock weight drive system. Their 'language' is no more difficult
to learn and use than is the vocabulary you already use as a
clockmaker--a deadbeat means something entirely different to you than it
does to the 'man on the street.'
4
Those parts of a weight line directly supporting the weight,
that run between the winding barrel (or a guide pulley3
at the top of the weight channel), and the weight, (or the pulley(s)
attached to the weight), have no specific names or definitions in
current horological dictionaries, merely those catch-as-catch-can terms,
such as double-compound, etc., mentioned already. These specific parts
of the weight line are used in calculating and defining the compounded
vertical weight drop and the mechanical advantage of the system, and
should be easily identifiable in terms easily understood by everyone who
works with either hoisting or clock drive systems.
A fall, or a part of line, is defined as that section of the
weight line between the weight, or the pulley(s) attached to the weight,
and the winding barrel, or the guide pulley(s) at the top of the weight
channel. The following nomenclature is proposed to define the degree
of compounding, as well as to bring the horologist's terminology on
weight lines into logical agreement with applicable modern standards and
methods as much as possible:
a. with one line at the weight:
single fall, or one part of line;
b. with two lines at the weight:
double fall, or two parts of line;
c. with three lines at the weight:
three falls, or three parts of line;
d. with four lines at the weight:
four falls, or four parts of line;
and so on, up through however many falls, lines, or parts of line are
found in the system. (Lord Grimthorpe wrote that a system with more
than three falls has excessive inherent friction losses, and that the
decrease in vertical weight drop is not sufficient to justify the
increased friction, heavier weight required, and the much longer weight
line of a system with more than three falls4.)
3 The common, or layman's,
term for a sheave or block.
The accepted technical terms for
the various parts of weight systems will be defined in the Glossary,
but familiar terms, unless they are not deemed appropriate, will be
used as much as possible throught this article. A moving pulley is
referred to as a 'running block'.
4 The decrease in required weight fall varies as
the reciprocal (1 divided by the number of falls) of the number of
falls; in other words, with a required vertical weight drop of 72 feet
for 8 days, a three fall (reciprocal of 3 = .3333) requires 24 feet of
vertical space (72 x .3333 = 24). The difference between the two falls
(36 foot drop) and 5 falls (14.4 foot vertical drop) is only 21.6 feet.
The increases in friction, length of rope, and weight required do not
justify the use of more than 3 falls excepting in unusual cases.
5
Figure 2. Common weight
line suspension systems.
Note that only supporting weight lines, those running directly to and
from the weight or the moving pulley(s) attached to the weight, are
counted in specifying the number of falls or parts of line. A
non-supporting weight line section, e.g., one which leads from the guide
pulley at the top of the weight channel to the winding barrel, even
though it transmits the effective force of the weight to the
winding barrel, should not be counted as a fall. In short, the number
of falls defines two different parameters. First, the total vertical
weight drop (Tvd) required, multiplied by the reciprocal (1
divided by the number of falls) of the number of falls yields the
compounded vertical drop (Cvd) of the weight line system.
Second, the number of falls determines the mechanical advantage of the
compounded weight line, which mechanical advantage is used by the crane
operator to lift a heavier weight load with comparatively little effort.
Unfortunately, the mechanical advantage acts against the clockmaker,
becoming a mechanical disadvantage, so to speak, requiring him
to use a heavier weight to achieve the required effective
weight for the clock drive system5.
It should be noted here that there is a definite difference in the
application of clock and crane rope and weight line systems: the crane
operator is interested in the short-term dynamics of safely lifting and moving
widely varying weights through widely varying distances; the clockmaker is
interested in the long-term dynamics of safely supporting a defined weight,
and in safely controlling its rate of fall through a
limited vertical space.
5 If the total
required drop is 72 feet with a 50 pound weight, a two fall system
requires half the vertical weight fall; (1/number of falls) = .5 x 72
= 36: but requires a 100 pound weight; 2 (falls) x 50 = 100.
For more accurate calculation of the total weight necessary to drive the
clock, see Appendix II/9.
6
The weight drives for household clocks can probably follow current
convention and use the terms 'weight cord', and 'weight cable' as well
as 'weight line', and 'pulley' rather than 'sheave' or 'block'. The
latter two terms are used by the crane and derrick operator, and are
considered the 'proper' technical terminology, but for the sake of
convention and that we are already familiar with and use the term
'pulley' rather widely, pulley will be used throughout this article to
avoid the possible confusion of three different words which refer to the
same item.
Weight Systems:
As an introduction to tower clock weight systems, consider first
some of the weight drives with which we are all familiar. The common
O.G. has a weight cord which runs from the winding barrel over a guide
pulley in the top of the case with a weight attached to the end of the
weight line.
The system in this case has a single fall, or single part of line
supporting the weight, so the entire force of the weight is felt at the
pulley and (less the friction losses) at the winding barrel.
Figure 3. Single fall
weight line system used in a weight-driven shelf clock.
7
The total vertical weight drop (Tvd) and the compound vertical drop
(Cvd) are equal.
The mechanical advantage is 1. The O. G. clock, with its
single fall, is designed to run (usually) for thirty hours before the
weight bottoms out in the case and the clock stops. A compound, or
multiple fall, system is used in the typical tall-case clock which is
designed to run (usually) for 8 days.
For all that it might sometimes look like a tangled web of ropes
and pulleys, a compound weight system is really a simple affair. For
instance, the weight line in the tall-case just referred to is attached
to the winding barrel at one end, and (usually) to the seat-board at
the other, with the driving weight suspended between these two points on
a pulley. The degree of compounding is 2 fall: the driving weight
has two supporting parts of weight line. In a 2 fall weight system,
the effective
driving force for the clock is one half of the actual weight and the
total drop of the driving weight is one half of what it would be if it
were suspended as is the O.G. weight.
Figure 4. Typical tallcase
clock weight line compounding.
8
The total vertical weight drop, [Tvd = 8 ft] required,
multiplied by the inverse (1/# of falls; in this case, 1/2 = .5) of the
number of falls yields the compounded vertical drop, [Cvd, = 4 ft]
of the two-fall weight line system. Note that while the weight itself
drops only four feet, eight feet of cable actually unwind from the winding barrel.
The mechanical disadvantage is 2;
each fall supports half of the total weight, therefore the weight
has to be twice as heavy as is the weight used with a single fall.
That's why a tall-case runs for 8 days with a four-foot weight drop,
(but with a heavier weight) without a lot of extra wheels (as in a month
or year clock) between the main (or great) wheel and the minute (or
center) wheel. The O. G. weight line setup in an otherwise normal
eight day clock would need a weight drop of 8 feet, with a weight half
as heavy. Lighter weights driving tall-case clocks might save a lot of
bottom boards in clock bases when the weight lines break, but we would
have to have either very tall clocks (and very high ceilings) or more
expensive clocks with more wheels--which would probably require heavier
weights--which would...why not just compound the weight line system?
O.G. and tall-case weight systems are simple and easy to understand,
as are the weight systems for most tower clocks, roughly 75% of which
are 2 fall systems. But how does the clockmaker, faced with an
unfamiliar tangle of weight lines, ponderous weights of half a ton or
more, and more pulleys than Cap'n Ahab6 had on board the
Pequod, deal with this seeming complexity? Common sense and some
elementary math will untangle all your problems on weight drive systems.
A small calculator will speed up your math a bit, but clockmakers had
it all figured out
6 Cap'n Ahab
would probably break out the cat o' nine tails if one of his sailors
were to use the word 'pulley' on board ship. Every profession has its
own vocabulary: on board ship a specialized vocabulary avoids confusion
when confusion is the last thing needed. Since the term 'pulley' is
familiar to the reader, the technical terms will be defined and
explained, but will not necessarily be used in the body of the text.
9
several centuries ago. But, before you even lay a hand on the clock,
do remember that tower clock weights and their weight lines (on which
more later) will be handled, at all times, with respect, great caution,
forethought, and, if necessary, advice or help from the professionals in
a local rigging company. The weight lines, if they are under working
tension, will always be handled in the same manner. Gravity might play
tunes on a musical clock, but it does not play favorites.
The logic in using a compound weight system is to allow the clock
a reasonable and pre-determined running time (with a reduced vertical
weight drop) with a reasonable amount of weight. Assume that the
clockmaker designed his tower clock to run for a week with a 50 pound
weight dropping 72 feet, but the church in which the clock will be
installed has only 25 feet of weight drop available. Several options
will be considered. It would be possible to copy the O. G. setup, and
suspend the weight on a single line from a guide pulley 70-odd feet up
in the steeple, but the chances are that a weight thus suspended will
invade otherwise inhabited areas in its descent, whether that invasion
is in a controlled manner, or in free fall, which latter tends to put
the inhabitants off their feed. With a single fall 25 foot weight drop,
the custodian would have to wind the clock every 2.88 days, but that
would wear out ratchets double-time, and he would probably complain. A
two fall rope system will double the running time to 5.76 days, but
will now need at least 50 feet of weight line, another pulley, at least a
100 pound weight, and the clock winder will probably still complain
that he has too much work to do too often. Once a week seems to be
enough for most folks, whether they're going to church, visiting the
in-laws, or winding a clock.
7 A single line
in a tower clock weight system will have two faults: the weight line
will tend to unlay, unless a special (more expensive) type of line is
used, and any small disturbance will tend to make the weight oscillate
like a pendulum.
10
Figure 5. Typical
three fall reeving diagram.
The clock winder will be much happier if a three fall system, with
two compounding pulleys, and three falls at the weight, is used.
Multiply 72 by .3333 (1/3 = .3333), and note that the clock now needs
only 24 feet of fall to run a full week, with a bit left over.
However, at least a 150 pound weight is now needed to drive the clock,
because there are three falls, and each one of those falls supports one
third of the total weight--the mechanical advantage is 3--the clock is
still being driven by an effective weight of 50 pounds. The addition of
a few extra pounds to the driving weight will compensate for the
frictional losses (see Appendix II/9) due to the two compounding
pulleys. The clock, amazingly enough, is still nearly as easy to wind
as it had been with a fifty pound weight (without any pulleys), because
of the mechanical advantage of 3 provided by the
11
compounding of the weight line system. The clock winder will have to
reel in 72 feet of line each week, and will also have to be fairly
punctual about winding the clock, because that one foot of weight drop
available after 7 days will only run the clock for another 8 hours8.
If the custodian still complains that once-a-week-winding is too much
work, we could install a 12 fall system, just to keep him quiet. The
clock will now run a week with a vertical weight drop of only 6 feet
(just over a month with 25 feet of vertical weight drop), but now needs a
600-plus pound weight, 300-plus feet of rope, and at least 11 pulleys.
The cost and complexity would skyrocket out of all proportion to any
advantage gained--even the winding barrel would have to be
redesigned--and Lord Grimthorpe's ghost is always there to remind us
that three falls are just right, the shortest weight fall with the least
friction. The time required to wind the clock with a 12-fall system
would be ridiculous--assume that the winder can spin the winding crank
at 6 turns per minute, and that the winding barrel circumference is 2
feet. He will wind the clock for a solid 25 minutes once a month, as
opposed to a mere 6 minutes each week with a three fall system.
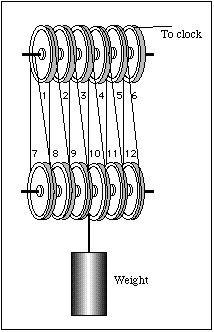
Figure 6. Reeving diagram
for a 12 fall weight line system.
A 12 fall weight line system can easily be installed, but somehow it
seems to be a bit less than practical.9
The design of a maintaining power system which would run the clock for
the 25 minutes needed to wind the clock would be a clockmaker's
nightmare. Might as well put in an electric clock.
8 I recently
worked on a tower clock that had a three-fall strike weight system and a
minimal amount of weight fall space available. Winding the clock just
after it struck 12 on Sunday meant that it had to be wound after
striking 12 exactly 7 days later--there just wasn't enough fall left for
the clock to strike 1, one hour later.
9 Ball bearing pulleys each contribute about 2% of
the total friction losses in a weight system. A 12-fall system will
require at a minimum, 12 pulleys. Friction losses would be on the order
of 24%. A clock designed to run with a 50 pound weight rigged with a
12-fall system would now require a 600 pound (12 x 50) weight, plus 24%
(144 pounds) for a total weight of 744 pounds. Bronze/brass bushed
pulleys (5 to 5.5 % friction) would require a 930 pound weight in a
12-fall system. No allowance has been made in either of these examples
to compensate for the loading of the outside dial hands due to weather,
or for the losses due to bending losses in the weight line. Determining
the correct weight to drive a tower clock is a totally empirical
process, otherwise known as a SWAG (Scientific Wild Ass Guess). For a
fuller discussion of determining frictional losses see Appendix II.
12
An odd method of compounding a weight line recently appeared in Tower
Talk, the newsletter of Tower Clock Chapter 134, which was referred to
as a 'winding aid'. To understand its operation, we have to make a
couple of assumptions for the sake of clarity, as far as various
diameters, circumferences, etc., are concerned. The clock winding
barrel is two feet in circumference, the large barrel is 6 feet in
circumference, and the small barrel is again 2 feet in circumference.
Referring to the diagram on the right below, 114. 5 feet of cable will
be required, but the clock will be able to run longer before the weight
bottoms out. Total cable length depends on the physical separations of
the clock winding barrel, the 'winding aid', and the pulley at the top
of the weight channel.
Figure 7. A comparison
of conventional compounding and an ingenious compounding method
for a weight system.
13
The differential in cable lengths is due to the 'winding aids' '
requiring two separate lengths of cable, while normal compounding can
use a single length of cable. The 'winding aid' was probably used
because it would provide for a slightly longer running time, and would
avoid the friction and cost associated with the three (extra) pulleys
needed for conventional 3-fall compounding. Disregarding friction, and
the half-diameters of the wire rope, this assumed 3:1 ratio will reduce
the force felt at the clock winding barrel to a third of the actual
weight, which will require that the weight be increased by a factor of 3.
In this case, to reduce the weight drop required, 2 fall compounding
would require a doubling of the weight, and would yield a total weight
drop of about 22.4 feet. Three fall compounding would yield a total
weight drop of almost 15 feet and the driving weight would have to be
three times as heavy.
Whoever designed this system had his head on his shoulders. He
realized that three fall compounding was out of the question because of
the limited weight drop available, and came up with an ingenious
solution that used a little more rope, and achieved the same end, with
less friction and expense for the extra pulleys. The need for a very
short weight drop is, I suspect, the reason this odd system was used.
Very simply, it reduces the overall complexity of a three-fall weight
system.
Multiple fall, or compound, tower clock weight systems are
simple in concept--and used the world over--but must
always be treated with caution. Compound systems provide the clock
with a mechanical advantage which allows it to run and strike for an
extended time with a reduced weight drop, yet require a much heavier
weight. The conveniences of the shorter weight drop and an extended
running time only come at the expense of the heavier weight, a longer,
more expensive weight line, more pulleys, increased friction, and a
tired, irritated, clock winder--there ain't no such thing as a free lunch.
14
Pulleys:
Pulleys are used in a weight drive system to make the rope load
uniform throughout the system. A pulley is also known as a sheave, a
block (a pulley or multiple pulleys housed in a common frame), or a
grooved wheel, and is critically essential to the proper and safe
operation of a weight-driven clock. Unfortunately, pulleys are usually
ignored. The general tendency of most clock owners is to re-use what
the clockmaker put in the steeple--sometimes as much as 150 years ago.
Chances are that the original cable was a natural fiber rope, and the
clock owner ends up putting in a "longer-lived and safer" wire rope
weight line system with cheap, inadequate, and unsafe pulleys.
Whatever the case, be very careful if you (re)use an old wooden pulley
for a wire rope--and caution the owner about the possible problems.
Wire rope on wood may work--for a while--but the wire will very soon
begin to cut into the wood, the pulley will wear badly out of round
(because of the grain), the thin flanges of the groove may break off,
the line may then slip off the pulley, and will either be seriously
damaged (probably kinked), or may do some other damage. A kinked wire
rope is an unsafe rope, and has to be replaced. A wire rope is safest
running on a metal pulley, either of cast steel or of cast-iron.
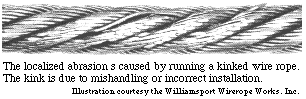
Figure 8. The localized abrasions
caused by running a kinked wire rope. The kink is due to mishandling or
incorrect installation.
15
A pulley is defined by its shaft diameter, the rope diameter for
which it is grooved, the outside diameter of the flanges, tread diameter
(the diameter to the base of the rope groove) and its pitch diameter.
Pitch diameter is the diameter to the center of the rope on the pulley,
i.e., one half the rope diameter plus tread diameter. Tread diameter is
the most critical parameter to be considered in the selection of a
pulley for a wire rope (steel cable). The ratio of tread diameter to
rope diameter is referred to as a D/d ratio. Optimal pitch diameter of a
pulley is determined by the ratio D = X x d, (usually written D/d)
where D is the diameter of the pulley, X is a Federal
specification/rope manufacturer10 recommended constant, and d
is the diameter of the rope. For instance, a given D/d ratio of 45,
for a 1/4, 6 x 18, fiber core rope, requires that an 11.25 inch
diameter pulley must be used for optimal rope life. The service life of
a 1/4 " 6 x 7 (much stiffer) rope would drop by about 55% if it were
used on a pulley this small. Wire rope bent 180° around a pulley is
stressed or fatigued each time it passes around the pulley. The smaller
the pulley diameter, the higher the stress or fatigue factor, which has
a direct bearing on rope life, rope strength, and on the safety of the
system. (See Appendix II/4) For this reason, American codes specify
fixed D/d ratios which are directly linked to rope size, rope
construction, and apply to both pulley and winding barrel diameters.
The recommended size for the groove in a pulley is 1/64 of an inch wider
than the nominal diameter of the rope. Too narrow a pulley groove
will prevent proper seating of the rope in the bottom of the groove, and
the uneven load distribution will damage the rope.
Figure 9. A. Illustrates a worn rope
in a worn groove. B. Illustrates a new rope in a worn groove.
C. Illustrates a new rope in a new sheave.
10 Federal
Specification RR - R - 571a specifies minimum drum and pulley diameters
in relation to rope diameters. Safe and proper operation of cranes and
derricks and other systems using wire rope systems are governed by
Federal, American Natonal Standards Institute (ANSI) amd manufacturer
standards, from which the OSHA standards are derived, and which are the
basis for this paper.
16
Too wide a groove will not provide adequate side support, and the
rope will tend to flatten. Specifications for crane pulleys require
that the grooves be smooth and free from surface defects, that a
retainer (guard pin) be fitted if the rope system might be momentarily
unloaded (as with the weights all the way down), and that pulleys be
equipped with a means to lubricate the bearing. Alignment of the
pulleys in the system must be checked, to avoid excessive wear of the
rope and the pulley flanges.
Friction losses (See Appendix II/9) due to the pulleys can
seriously affect a tower clock weight line system--losses with common
bronze-bushed pulleys are on the order of 4.5 to 5.5 per cent., and
those from precision ball or roller bearing pulleys about 1.5 to 2 per
cent. Total friction losses are affected by the construction of the
rope, pulley bearing types, and the ratio of pulley-to-rope diameter.
Imagine how much drag is created when the rope installer, trying to save
a few dollars, reuses the old unbushed, too-small, wooden pulleys
installed in the steeple and over the weight chutes 150 years ago. A
great deal of weight has to be added to overcome the extra drag.
Incidentally, the total lack of any safety considerations in the reuse
of some wooden pulleys with wire ropes is appalling. I have removed
badly cut, worn and wobbly wooden pulleys with the groove flanges broken
away, still at work 150 years after the clock was installed, with
several hundred pounds of stone looking very much like the Sword of
Damocles. However, it is a shame to remove the original wood pulleys
from a two-hundred year old clock--if the pulley has an adequate D/d
ratio. If the groove is in good condition, and the pulley is rebushed
correctly--the pulley can probably be safely used--for a while. If this
is done, make sure that the custodian (or you) checks these pulleys
periodically to ensure that they remain in good condition. It is
possible (indeed, recommended, if the pulley is to be retained) to fit
the groove of some of these wood pulleys with a suitably formed sheet
metal hoop, to avoid the cutting of the wood by the wire. The wooden
pulley should only be reused if it is in good condition, and its radial
loading (See Appendix II/6) will not exceed 200 pounds. There is no
specific data available on radial loading limits for wood pulleys; the
above is an empirical value derived from experience with several weight
systems using wooden pulleys.
17
Radial loading of a pulley should be limited to 500 psi for cast-iron,
and 900 psi for cast steel11.
Pulleys may have a bushing of bronze (high friction) or ball/roller
bearings (low friction) and should have some easily accessible means of
lubricating the bushing or bearing. Lord Grimthorpe (and, incidentally,
the Howard instruction sheet posted in many clock rooms) recommend
lubricating the pulleys annually. Personal experience suggests that
once every six months is better. Pulleys and blocks should have a guard
installed to keep the rope in the groove, in the form of a pin or a
bolt through the cheek-pieces which will just clear the rope when it is
seated firmly in the groove. The purpose of the guard pin is to keep
the rope in place if the rope is completely unloaded.
Under no circumstances should you ever use a cheap pulley made up
of two separate stamped pieces of steel spot-welded together, or one
with a formed sheet metal rim (sometimes called a gin pulley). An
inadvertent shock load can split the former, and can seriously deform
the latter. Do not use the typical hardware store pulley--they are too
small, and they will break. It is not an afternoon's light
entertainment to wrestle with a 300 pound weight jammed three quarters
of the way up the weight chute because the rope slipped and broke a
pulley while you were working on the weight system. If you find
yourself in a situation such as this, unless you have the tools and the
expertise, it is best to call in the riggers. It's also a safe bet
that a mistake like this will only happen to you once!
|
Always let a weight all the way down before releasing either
end of the cable from its fastening, indeed, before doing any work on
the cables or the pulleys.
(Any time the weights are to be let down--which puts
all of the weight on the winding crank--have an assistant in the clock
room to release the ratchet(s). Don't try to do it all alone. It is
impossible [and not too smart to try] to stop a runaway winding crank.
There is no way of stopping a runaway weight, since a clock winding
barrel doesn't have a brake of any sort--something that makes OSHA very
nervous.12)
|
11 Radial pressure
can be computed using the formula given in Appendix II/6.
12 Standard practice on cranes is that the drum
have a brake capable of holding the load without any other
locking/holding devices. Crane drums are also dogged if the crane
operator is not present, however temporary his absence.
18
If the barrel end of the
rope has to be disconnected, keep some tension on the rope leading to
the weights with a bungee cord, which will keep the rope in the pulley
grooves (particularly if the pulleys have no guard pins), and may avoid a
loose and possibly kinked rope in the weight channel. Before you
wind up the weights, if the rope has been unloaded, carefully check all
pulleys in the system, and make sure the rope is correctly seated.
Dropped and jammed weights, ruined ropes, broken pulleys, damaged
fingers, and damage to property are constant and expensive reminders
that gravity is always lying in wait for the unwary and the careless.
Common sense and safe procedures are the best means to avoid its deadly
potential. If you don't know how to do it--ASK! Also: THINK!
Winding barrels:
(A) Diameters:
The rigger and the crane operator consider the diameter of the drum13
on which the rope is wound to be critical to the life of the rope.
Most clockmakers don't even think about it. It's a relatively simple
matter for the crane operator to change the drum diameter on his
machine, while the clockmaker is locked into using the winding barrel
(whose diameter is usually too small according to modern standards for
wire ropes) provided by the maker of the clock. Any change in the
barrel diameter on a clock requires careful recalculations of the weight
needed to drive the clock, the amount of rope needed, and the crush
resistance of the material used to increase the barrel diameter.
However, a too-small barrel diameter will materially decrease the life
of the rope, because of the bending stress incurred as the rope winds
around the barrel. Nearly all tower clocks, particularly the very early
American clocks (before 1875) have rather small diameter winding
barrels--some as small as 7 inches. The clock owner, and the clock
custodian, should be made aware of the problem and should be cautioned
about inspecting the rope regularly if it is used on an undersized drum.
The D/d ratio mentioned above applies to drum diameters as well as to
pulley diameters.
13 The technical
term is 'drum'; as clockmakers we will use the more familiar 'winding
barrel'. Crane drum diameters are usually increased by devices known as
'laggings', which are usually designed for a specific machine.
19
Even though changing the barrel diameter will take away from the
originality of the clock, there are many clocks with too-small barrels,
which could benefit in several ways by such a change. The driving
weight could be reduced considerably. For example, if a clock is driven
by a 100 pound weight with two falls, the force at the barrel is 50
pounds14. Given a barrel radius of 4 inches, and a great
wheel pitch radius of 12 inches, a force of 16.7 pounds is felt at the
pitch radius of the great wheel. Increasing the radius of the barrel to
8 inches would permit reducing the driving weight to 50 pounds. (This
may seem to be a tremendous change in diameter but the D/d ratio for a 6
x 19, 1/4 inch wire rope (D = 45 x d), means a minimum drum diameter of
11.25 inches.) There is a point of no return in increasing the barrel
diameter, but there are benefits. A reduction in the driving weight,
the weight rating (and the cost) of the wire rope, and the ratings of
the pulleys, as well as the reduction of stress on the rope, are a few.
Changing the barrel diameter is only mentioned here as a possible
course of action if there is severe stress on the wire rope due to a
too-small barrel, but is not a blanket recommendation. If the barrel is
indeed too small, very careful consideration of the type of rope is
recommended. The most flexible rope should be chosen--such as a 1/4
inch, 6 x 37 (Extra Flexible Hoisting Rope)--and then monitored very
carefully. The D/d ratio for 6 x 37 wire rope is 27d, which means that
a 6.75 inch pulley or barrel can safely be used, although the rope is
much more expensive than the more common 6 x 19.
(B) Capacities:
If we assume a clock winding barrel about 2 feet in circumference, and
about 18 inches long, an assumed 144 feet of quarter-inch wire rope can
be wrapped on the drum. However, life never works quite that neatly.
The formula for computing the actual amount of rope that can be put on a
given winding barrel is:
L = (A + D) x A x B x K, where: (in this case:)
A = nominal rope diameter, (.25")
D = diameter of barrel, inches, (7.639")
B = width (or depth) of barrel, inches (18")
K = appropriate factor from table below: (3.29)
which yields a figure of 116.8 feet.
Rope Dia. (in) | Factor |
3/32 (.094) | 23.4 |
1/8 (.125) | 13.6 |
3/16 ).1875) | 6.14 |
1/4 (.25) | 3.29 |
5/16 (.3125) | 2.21 |
3/8 (.375) | 1.58 |
7/16 (.4375 | 1.19 |
1/2 (.5) | .925 |
14 For a full discussion
of the forces applied to clock winding barrels, main wheels, etc., See
Gravity Drive in Large Clocks by Charles K. Aked
(BULLETIN of the NAWCC, #261, Pg. 316.)
20
In no case should there ever be more than one layer of weight line on
a clock winding barrel. A longer rope may reduce the repetition
frequency of the clock winder's task, but damage to the rope and to the
clock may be the result. An over-long rope which winds on the barrel in
two layers increases the effective weight (it becomes a crude sort of
two-step fusee). The flanges on most clock winding barrels are rather
low, and may allow the second layer of rope to overrun the flange, and
fall on the outside of the flange15. If the rope overruns
the ratchet/click end of the barrel and then jams in the click on the
great wheel during winding--it's happened--a rather mundane task
immediately becomes very complicated.
Weights:
Before installing a new weight line system, you need to know what
weight load will be placed on the rope and the pulleys; in working with
an existing system it's smart to know how much weight you are dealing
with. It definitely builds up the respect factor. In the usual factory
clock installation16 the overall weight is fairly easy to
calculate as the clock weights are usually made up of metal plates or
blocks; merely weigh one of the plates or blocks, count up the plates or
blocks that make up each weight, and multiply. It is very strongly
suggested that the weights be let down as far as possible (i.e., all the
way) before doing any checking. |
(Any time the weights are let down--which puts all of the
weight on the winding crank--have an assistant with you in the clock
room to release the ratchet[s]. Don't try to do it all alone. Too many
things can go wrong.)
|
Other clock weights are slightly more difficult to calculate,
particularly those which are boxes filled with broken-up pieces of cast
iron, stones (rubble), or sand, but a close approximation can be made
by calculating the volume of the weight box, and weighing a cubic foot
of whatever was used to fill the box. Don't forget to weigh the weight
box itself, and the pulley(s) immediately above it--they are all parts
of the total driving weight17. A solid weight will usually
be granite, soapstone, marble, sandstone, or cast concrete.
15 Double rope
layers were common on many of the very early clocks, and their makers
made provision to turn the rope back on the winding barrel rather than
have it ride up on the flange. For an example, see BULLETIN #302, Pg.
291; The Great Clock at Chartres.
16 It should be noted that not all factory
installations use the commercially made weights. A round-top Howard
in Andover, Maine has rubble-filled wooden boxes. The strike weight is 3
feet by 3 feet, by 2 feet deep. Other weights noted have been an old
copper water tank filled with sand, and cast concrete blocks and
cylinders.
17 The weight of the wire rope itself, as it runs
off the winding barrel, can be a factor in calculating overall weight,
but in most cases can be safely ignored. For instance, 1/4 inch wire
rope weighs .1 pound per linear foot.
21
Measure the weight--length, width, and depth--multiply those figures (in
inches) to derive cubic inches; divide that figure by 1728 (cubic
inches in one cubic foot) and multiply by 16018. 160 pounds
per cubic foot is a fairly close approximation of the actual average
weight per cubic foot of most rocks. A bit of interpolation, or several
sets of measurements, will sometimes be necessary to calculate the
volume of the rock, if the rock is irregularly shaped. Experience has
shown that in most cases, because of the irregular shapes of rocks used
as weights and the difficulty of identifying some dust- and
pigeon-dropping-covered mineral specimens, 160 pounds per cubic foot is
an accurate figure. I've used different types of scales (from bathroom
to steelyard) to weigh various stone clock weights, and find my
calculations are usually within five pounds, if I've measured the weight
correctly. (See Footnote 18 or the Glossary for more exact
information on weight per cubic foot for various rocks.) A spring
scale--such as a fisherman's scale--attached to the weight line in such a
manner that it is pulling against the weight might seem to be a good
idea, but the spring scale will also read inertial and frictional losses
of the pulley system as 'weight', so the reading will not be accurate
(See Appendix II/9). Spring scales aren't very accurate in and of
themselves anyway, and a spring scale that will register 150 pounds or
more will be rather cumbersome. If it isn't absolutely necessary to
haul something up a 30 foot ladder, it probably doesn't belong in the
clock room. It's worth noting that inertial loads and pulley friction
losses can cause an apparent error of as much as 33% in calculating the
weight of a load on a crane, therefore the spring scale may read an
apparent weight load that doesn't really exist. The wide variation in
apparent load (resulting from inertial and frictional effects) is based
on rope load indicator readings taken while lifting and lowering a known
weight and are a best-guess19 (it is difficult to say what
is inertia, and what is friction) calculation based on the loading of a
rope making a 180° bend over a pulley.
18 Various
weights per cubic foot for different types of solid rocks and other
materials are: bricks,125; cement, 137: granite, 168; limestone, 162;
marble, 168; sandstone, 143; slate, 175; soapstone, 168; gravel, 109;
sand (dry), 100, rubble (small rocks) 90.
19 The variation in rope load indicator readings
is known as hysteresis by makers of these indicators.
The indicators are usually calibrated
to read true load during lifting, which means that they compensate for
both pulley and bending load friction losses
22
Figure 10. A method of preserving
an old stone weight. The two holes seen on either side of the upper
cross-brace once held a 'staple or 'dog' joining two stone blocks. The
original hook embedded in sulphur is still in use, and is now welded to
the cage.
With the weight all the way down for measurement or for weighing,
carefully check it for any structural problems--loose bolts, nuts, worn
hooks, cracked plates, etc. If the weight is a rock, examine the
embedded hook20. 19th century stonemasons very often set the
hook in the rock with molten sulphur, which avoids dissimilar-metal
electrolysis at the base of the hook. The danger here is that if the
sulphur gets wet, the hook may be weakened by the action of the
sulphuric acid which then forms. Some hooks are set with lead or zinc,
metals which have a tendency to creep under a continuous load. Any
looseness of the hook, cracks or spalling of the immediate area around
the hole, or any other evidence that the stone/hook connection might
fail is sufficient reason to remove the weight from service. A strong
strap steel frame with a new hook will preserve the originality of the
clock weight. While the weights are down, check the pulley(s) just
above the weight. Old wooden pulleys should be carefully checked; they
will probably need to be rebushed, and may be cut if they have been used
with a wire rope. If the old pulleys are in such bad condition that
they can't be salvaged, either cast-iron or cast-steel pulleys of an
appropriate diameter should be installed. Also check the termination
of the weight line--if it uses a thimble and U-clips (known as Crosby
clips), make sure that they are installed correctly, and made of the
proper materials. Correct installation and material information will be
found later under the heading of Rope End Fittings. Also
check the lubrication of the rope. The first few feet of weight line in
the weight channel are rarely checked or lubricated, simply because
they are usually located in areas with difficult access.
More information on proper lubrication will be found under the heading of
Lubrication:.
20 Some stone
weights are made up of more than one section. The sections are held
together by 'dogs'--shaped like a large staple--again, set with molten
sulphur. Check the security of the dogs as well.
23
Figure 11. An old
granite weight with molten-sulphur-secured hook and a wood pulley used
with wire rope.
Note the visible wear in the groove of the pulley.
Why is it necessary to check the weights and pulleys on a tower
clock? In one word, safety. If a weight line is to be replaced, you
have to know the weight the new line must support. You may also find
that the clock time train is seriously over-driven, whether
deliberately, or inadvertently21. The time side weight is
traditionally the lighter weight, whether the clock is an O.G. or a
tower clock--but some makers threw tradition out the window, and the
heavier weight will be on the time side. A simple visual examination
should tell you whether an unscrupulous (or unconscious) repair
type--I've seen it happen--has switched the weights, to cover a fault in
'repairs' to the time side. Usually the clock doesn't strike very well
if this has been done, but then some tower clocks aren't allowed to
strike at all, so this situation may go undiscovered for years22.
Occasionally one of the driving weights has had extra plates or
blocks, extra cubic feet of sand or gravel, or lengths of railroad track
added for a similar reason--usually more weight than is needed to
compensate for friction losses. The idea seems to be that if a small
amount of extra weight makes the clock run well, then a lot is even
better--never mind that the clock hasn't been cleaned in twenty years or more.
This "if a little is good then more must be better" syndrome is
fairly common amongst clock custodians. It also appears when a clock is
oiled: if a small amount of oil is good for the clock, then a lot of
it ought to be even better. This is when oil gets poured on the
wheels--car transmissions run in oil, don't they? They do, but those
transmissions are designed with different tooth forms, they have
different loads to handle, and don't have dust settling on them 365 days
a year. At the opposite end of the oil spectrum is the electrified
clock--most of them are oiled but once a year. A neglected,
electrically re-wound clock was found to have six inch curls of dirt and
dried oil extruded from the time train bushings when a local town
complained that their clock didn't run very well. More weight was the
custodian's solution to the problem; a solution which didn't work for
very long. Or very well, either. This same custodian had tried to set
the outside dial hands ahead by moving (and breaking off) the minute
hand on the internal setting dial. It has been noted that the "if a
little is good then more must be better" syndrome does not apply to the
inspection of wire rope weight lines--they are usually ignored. The
lack of inspection is not done with malicious intent; it is more likely
that no one ever bothered to inform the custodian of the need to
inspect the rope on a regular basis.
21 The alert
reader will have by now noticed that the determination of the proper
weight needed to drive a tower clock is almost invariably empirical.
Variables such as the loading of the outside dial hands, degree of
cleanliness of the clock, improper lubrication, the wrong type of weight
line, too-small pulleys, etc., simply cannot be plugged into a single,
simple formula. It is possible to derive the ideal weight to
drive a tall clock (see Penman, Ppg. 34, 35), but weather and neglect (a
dirty, poorly maintained clock) are unknown variables in a tower clock.
22 The author noted an innovative method for
calculating the strike weight for a Holbrook tower clock in Vermont.
The custodian had people of various weights hang from the weight line
while he checked the action of the strike train. His petite wife, times
two, plus 10%, was just right!
24
Wire ropes:
Wire ropes are the current weight line of choice for most weight-driven
tower clocks, usually because the
Figure 12. Typical construction
of a 6 x 31 wire rope with a fiber core.
Illustration courtesy of Williamsport
Wirerope Works, Inc.
owner of the clock is looking for a longer lived, less expensive (in
the long run), and safer system, or because wire rope was installed by
the clock manufacturer. Properly installed and maintained wire ropes
will last almost forever, but there are exceptions: witness the sitting
judge in the Aroostook County Courthouse in Houlton, Maine, whose
magisterial demeanor disappeared abruptly when his courtroom was the
fleeting host to a 1300 pound strike weight which crashed through two
floors and set off the building's sprinkler system when its wire rope
broke23.
Figure 13. The three basic
structural components of a typical wire rope.
Illustration courtesy of Williamsport
Wirerope Works, Inc.
The most common wire rope is known as Standard Coarse Laid Rope.
Many sizes, grades, and classes of wire rope are made for special
purposes, but a digression into these myriad types is not needed, simply
because they are rarely used (or appropriate) on tower clocks, and are
therefore not pertinent to this discussion. Wire rope is laid up in a
helix, not twisted, from individual wires into multiple-wire strands,
and these strands are then laid over a core to form the rope24.
The most common construction is a right-hand lay, which is to say that
the wires in each strand spiral to the left, while the strands spiral
to the right. Left-hand lay is just the opposite, and Lang laid rope
has both the wires in each strand and the strands spiralling in the same direction.
23 After he had changed his clothes
and regained some of his composure, the judge announced that as long as he
presided in that court, the strike side of the clock was not
to be wound. Popular legend holds that some of the expressions the
judge used are not to be found anywhere in the pages of Blackstone, but
were a simple reversion to the non-technical and somewhat more direct
and colorful speech of his French and Anglo-Saxon forbears.
Little wonder.
24 The exception to this general construction is
flat wire rope, made up of several 4-strand wire rope units stitched
together with soft steel sewing wire.
25
The rope core may be fiber (FC), wire strand (WSC), or independent
wire rope (IWRC). Most wire rope today is preformed, which is to say
that each individual strand is preformed into a helix, and thereby, each
individual wire, before it is laid into the rope. Standard Coarse Laid
Rope, 1/4 inch, 6 (strands) x 18 or 19 (wires in each strand), F(iber)
C(ore), right-hand lay, is the rope almost invariably found on tower
clocks, although it is occasionally incorrectly installed, on which
more later. This rope has a relatively large number of small wires,
thus serious attention should be given to whether the rope will be
chafed or abraded in normal use, the intention being to avoid serious
reduction in the strength of the rope. 1/4 inch, 6 x 18 or 19, fiber
core, right-hand lay rope--the most common--(I've found it on an 1873
Howard installation), made with Improved Plow Steel (IPS)25,
has a breaking strength of 2.75 tons. The rope weighs .1 pounds per
linear foot. The rope that is finally chosen for the installation
should provide a safety factor of at least five26. In other
words, the maximum effective weight driving the clock should not exceed
one fifth of the breaking strength of the rope. This means that the
total load on any single part of a rope which has a breaking strength of
2.75 tons (5,500 pounds) in a multiple fall system should be no more
than 1,100 pounds. Various grades of plow steel are used in the
manufacture of wire rope, ranging from mild plow steel (2.07 tons),
plow steel (2.4 tons) to extra improved plow
Figure 14. The most commonly
encountered wire rope structures. The bottom picture illustrates one
lay of the rope as a unit of measure peculiar to wire ropes.
Illustration courtesy of Williamsport
Wirerope Works, Inc.
25 Plow steels,
in grades ranging through plow, mild plow, improved plow to extra
improved plow, are high-carbon (.45 to .80%) steels, "made in an
exacting process", used primarily in in the manufacture of wire ropes.
Modern nomenclature is: for improved plow steel, Level 3 steel; extra
improved plow, Level 4 steel; however, both nomenclatures may be
encountered.
26 Federal regulations require that the rated load
divided by the number of parts of rope (or falls) shall not exceed 20%
of the nominal breaking strength of the rope; in other words, the
safety factor is 5.
26
steel (2.9 tons). Galvanized rope generally has a breaking strength
that is 10% lower in each grade, and is not recommended. If the owners
of a clock are assured that galvanized rope (which is more expensive) is
safest, they are perhaps being gently misled into believing that the
rustproofing eliminates any possibility that the rope will ever rust.
Galvanized rope is indeed the least likely to rust, but most clock
owners place such blind faith in the galvanization that the rope is
rarely, if ever, inspected. The zinc coating may either wear or flake
off the steel wire, which then begins to rust--usually inside the rope,
where it cannot be seen. Stainless steel wire rope is also available,
but is not recommended, simply because blind faith in so-called
rust-proof wire rope may well result in finding the weight in the cellar
with a busted bit of rope attached, because the rope was never
inspected. It should be noted here that a wire rope with rusted wires
in its core will require more weight to drive the clock. The roughened
rusty wires are no longer able to slide easily past one another as the
rope bends over a pulley, and the rust will abrade the internal wires
when the rope is bent under a load. A symptom of a lack of lubrication,
heavy loads, and small amplitude vibrations in the wire rope is known
as 'rouging'. Rouging means that abrasion is occurring between the
wires and strands, and that only small particles abraded from the wire
are rusting.
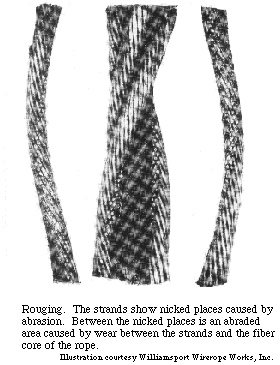
Figure 15. An example of 'rouging.'
The strands show nicked places caused by abrasion. Between the nicked
places is an abraded area caused by wear between the strands and the
fiber core of the rope.
(For more detailed information, see under Lubrication:)
Illustration courtesy of Williamsport
Wirerope Works, Inc.
27
The safety factor of five is used in the world of the rigger and the
crane operator, whose operating cables undergo much more severe stresses
and strains, as well as constant exposure to the elements. Careful
consideration of the construction and design of the weight system may
make it possible to use a lesser grade of rope, and less expensive
pulleys. However, better safe than sorry--don't ever rig a weight
system with a rope (or pulley) safety factor lower than five.
The weight the rope will support must be known before a proper
selection can be made. In making the final choice the following rope
properties should be considered: strength, which is a function of grade,
size, construction, and core material; flexibility and resistance to fatigue,
which are both greatest in ropes with a large number of small wires,
ropes with a fiber core, Lang laid ropes, and ropes which are pre-formed;
abrasion resistance, which is better in ropes made of larger wires,
but which varies somewhat according to the rope's construction;
crushing resistance,
which is greatest in wire strand or independent wire rope cores.
Flexibility and resistance to fatigue criteria are second only to
breaking strength in requirements for a tower clock, since there is
little likelihood that the rope
will be abraded or crushed if it is correctly installed.
Figure 16. An illustration of a crushed wire rope.
Illustration courtesy of Williamsport
Wirerope Works, Inc.
An extra flexible rope, even though it will be more expensive
initially, should be seriously considered if the clock winding barrel
diameter is too small. The selected rope size (diameter) will have to
be considered in the selection of pulley sizes and materials.
28
Proper installation of the wire rope is critical to its weight
carrying ability, its life, and the overall safety of the system. The
rope should not be kinked, which will seriously weaken it. Any kinked
rope (even if it is brand-new) should be immediately discarded, and
replaced with new, unkinked rope.
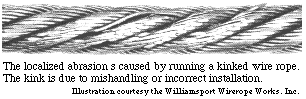
Figure 17. an illustration of a wire rope that has been
used after being kinked..
Illustration courtesy of Williamsport
Wirerope Works, Inc.
Don't try to splice in a new section of rope, it is not a safe
practice. It's a good idea to call the clock owner's attention to
kinked ropes, because they aren't safe. To correctly install a new wire
rope, it's best to reel the new rope onto the clock winding barrel from
the supply reel (this avoids twisting the rope), making sure that the
cable goes on the winding barrel bent in the same direction as it was on
the supply reel. If a pre-cut length of rope is supplied in a coil,
the coil should be unrolled along the floor as it is wound on the
winding barrel, again making sure the rope is bent in the same direction
on the winding barrel as it was in the coil. Bending the rope in the
opposite direction stresses it unnecessarily. The rope must also have
the proper construction, or lay. If the rope passes over the top
of the barrel as it is wound on the barrel (an overwound barrel), a
right-hand laid rope must be fastened to the right-hand side of the
barrel, and a left-hand laid rope must be fastened to the left side of
the barrel. If the rope passes under the barrel as it is wound
on (an underwound barrel) a right lay rope must be fastened to the left
side of the barrel and a left lay rope must be fastened to the right
side of the barrel.
29
Disregard of (or more likely, a lack of information about) this
requirement is the reason many clocks have the wrong type of wire
rope--it has the wrong lay--on their winding barrels. (The same
criterion applies to household clocks as well, but is not quite as
critical.) A rope with the wrong lay with regard to its attachment
point on the barrel will not spool on and off the barrel as smoothly and
evenly as it would if it had the correct lay, because successive wraps
will tend to chafe against one another. Check the winding barrels and
their attachment points before you order the wire rope, or make sure the
rope is correctly attached to the barrel according to the rules for
over- or underwound barrels. Try to avoid any reverse bends in the rope
during installation, and in reeving (stringing) the pulley system,
because a reverse bend stresses the rope unnecessarily. Reverse bends
may be impossible to avoid simply because of constraints imposed by the
construction of the building in which the clock is housed. If a reverse
bend in the rope is necessary, then do the best you can, with a large
diameter pulley at the point of the reverse bend, and very seriously
consider using an 'Extra Flexible Hoisting Rope'.
There are so many different types of winding barrels, ranging from
wood to cast-iron, with so many different methods of attaching the wire
rope to the barrel that the best course of action may be to ask someone
who is familiar with wire rope how best to attach the rope to the
barrel. Socketing or clamping the rope are considered the ideal
methods. (If a wire rope is to be installed on a wood barrel, the wood
should first be covered with sheet metal, because the wire rope will cut
the wood surface.) Most companies selling wire rope are quite free
with all sorts of good advice--just make sure that your source of
information is not a salesman who has a mere smattering of knowledge and
is looking for his commission--remember, an expert is usually a
salesman 100 miles away from his home office. The best means of
terminating a wire rope for attachment to a barrel is a ball (which fits
in a cavity in the barrel) swaged or zinc-soldered on the barrel end of
the rope, but this may interfere somewhat with reeving (stringing) the line.
30
The line may also be securely clamped to the surface or the flange of
the barrel, but tying a knot in the end of the line (which reduces the
breaking strength by 20%), or nailing the rope to the barrel are not
recommended. A wood barrel may have a hole bored all the way through
the barrel, with a socket cut to accommodate the terminating device. A
hardened two-piece ball for the barrel end of the rope is available. An
outer casing is slid over the end of the line, and a conical wedge is
then driven into the center of the line, to trap the strands against the
outer casing; however, this termination will reduce the breaking
strength by at least 20%. It is always a good idea to be sure that at
least two wraps of weight line are left on the winding barrel when the
weight is all the way down--preferably three. The friction of the line
wrapped on the barrel and the tangential angle of pull help to keep the
barrel end of the line where it belongs. A weight line pulling radially
from the surface of the barrel because the line is too short will
usually pull the end out of, or off of, the barrel, more often than not
with rather dire consequences. Standard crane practice is a minimum of
"two full wraps remaining on the drum with the hook in its extreme low
position."
Most tower clock installations route the line weight from the barrel
to a (usually) conveniently (sometimes, apparently randomly) located
lead (or first) pulley to redirect it toward the top of the weight
channel, where another guide pulley may be found. The proper location
and the alignment of this first pulley are critical to the maximum life
of the weight line, and to the even winding of the line on the barrel
when the clock is wound. The centerline of this guide--or more
properly, fleet--pulley should be aligned with the centerline of the
barrel. When the weight line is at either extreme end of the winding
barrel, the fleet angle (which is the angle between the pulley/barrel
centerline and the wire rope at its extreme deflection) should not
exceed 2°. 1 1/2° is the preferred maximum angle; 1/2° (or 30 minutes)
is the preferred minimum angle. A 1 1/2° fleet angle allows the line
to spool evenly on the barrel without any separation between turns, and
avoids interference with, and possible damage from, the sides of the
groove in the pulley. Anything less than a 1/2° fleet angle will tend
to make the line bunch up at one end of the barrel.
31
Figure 18. Fleet angle diagram.
The fleet angle should be limited to 1 1/2° if the winding barrel is
smooth, no more than 2° if the barrel is grooved. If the lead pulley
must be installed very close to the clock, due to space constraints, use
either a pivoted 'fleeting pulley' which can swing from side to side,
or a 'fleeting sheave'; a grooved wheel mounted on a horizontal shaft.
Both the fleeting pulley and the fleeting sheave must be mounted close
enough to the drum, or so constructed that a minimum 1/2° of fleet angle
is provided at maximum 'layover' of the fleeting pulley, or maximum
lateral deflection of the fleeting sheave on its shaft. Don't try to
use either the pivoted fleeting pulley or the fleeting sheave to change
the direction of the line to lead it to the top of the weight
channel--use another pulley farther away from the clock. A misaligned
or misplaced fleeting pulley or sheave may cause the successive turns of
line to chafe as they wind on or off the barrel, or will chafe the line
on the edges of the pulley groove, both of which wear the line
unnecessarily. Calculating the fleet angle is rather simple--no higher
mathematics are involved--because someone else already did it for you.
Merely divide the depth (some call it width) of the winding barrel by 2,
and then divide this figure by .03527. An 18 inch (1.5 foot)
deep barrel, divided by 2 is .75 feet. .75 divided by .035 equals 21.43 feet.
The rule of thumb in the crane operator's world is 1.25 feet
of separation between the barrel and the first, or main, pulley for each
inch of barrel depth or width28. If the fleet angle is too
great, the line tends to bunch up in the middle of the barrel, and may
chafe on the sides of the pulley groove when the line is forced toward
the side of the barrel. Too small a fleet angle will allow the line to
bunch up on one side of the barrel, or the line will
27 Trigonometrically,
you're solving for the adjacent by dividing the opposite (1/2 the drum
width) by the tangent of of 2 degrees (.03492, rounded to .035).
28 Note that this rule of thumb calculation uses the
entire width of the barrel, not one half of the barrel
as in the trigonometric calculation.
32
Figure 19. Typical
fleeting pulleys and fleeting sheave..
chafe against a preceding turn as it spools on the barrel. The
majority of tower clock installations don't have correct fleet angles,
simply because there isn't enough room available in most steeples. Most
clock rooms and steeples are a lot less than 21 feet wide, and many
have limited space below the clock room floor. The best advice is to
do the best you can with a pivoted pulley or fleeting sheave, and to
watch the line during winding, to make sure it winds across the barrel
as evenly as possible. Either the fleeting sheave or the pivoted pulley
work very well, although some clock owners will complain at the extra
cost. Remind them that it is a safety consideration, and that busted
ropes can mean busted budgets. Tell (many times!) the custodian that it
is not ever a good idea to try to guide the line onto the barrel with
his fingers; his fingers will likely be stabbed by a broken wire, and
if he somehow (these people can do some weird things) manages to get his
fingers trapped by the line, it's going to be a bit difficult for him
to release the ratchet to unwind the cable and release his fingers.
Rope End Fittings:
Figure 20. Two clips--A 'fist' clip at the left,
a Crosby clip at center, and a thimble at right.
Clamping the end of the cable to form a loop, or eye, at the dead end
(away from the barrel) also has its rules and proper methods. If a
Crosby clip (U-bolt clip) is used, the saddle of the clip should bear on
the live (weight-bearing) part of the rope, and the U (or bolt) portion
on the dead part. The U-clip saddle must be made of forged steel.
Installing the bolt on the live portion of the rope may cut or kink the
cable, which poses all sorts of dangers. For 1/4 inch cable, two 7/32
inch clips must be used, spaced at least 3 1/2 inches apart. The nuts
on the U-bolts must be re-tightened an hour after the wire rope is put
under load, because the rope will stretch--and its diameter will
decrease toward the nominal.
33
The fist clip is recommended, as it will not cut or kink the wire rop.
A clamped eye (any eye) must always use a thimble. The strength of a
properly made eye (with fist or Crosby clips) is rated at 80% of the
nominal breaking strength of the rope; something to consider when
figuring the safety factor and the total load on the rope.
In practice, any cable termination, other than a swaged or zinc-soldered
termination29, must be assumed to have only a strength
rating of 80% of the rope's rating, therefore, calculate your safety
factor accordingly. For instance, the load rating of the rope under
discussion (Standard Hoisting Rope, 1/4 inch, 6 x 18 or 19, FC, right-
or left-hand lay) drops to no more than 875 pounds with any termination
other than those which are properly swaged or soldered. Remember that
courtroom in Maine.
Safety Considerations:
After replacing a rope, and before you leave the clock room, it is a
good idea to wind the drive weights all the way up, let them all the way
back down, and then rewind the clock again to make sure the ropes wind
on and off the barrels evenly and that the ropes are correctly rove
through all the pulleys. Also check for a condition called 'block
twisting' or 'cabling'. When the wire rope is first loaded, it may tend
to untwist or unlay slightly, and then take a set. When the rope is
later unloaded, the pulley assembly at the weight may twist--up to
180°--which may tend to tangle the ropes. (This may also happen with
the rope loaded.) Merely rotate one end or the other of the rope a turn
or two (the apparent 'twist' will be reduced or eliminated), load the
rope and wind the weight all the way up and then back down, and check
for any evidence of 'cabling'. Repeat as necessary. It is possible to
use a suitably strong turnbuckle just above the weight. The turnbuckle
can then be adjusted to remove any of the effects of cabling.
|
(Any time the weights are let down--which puts all of the
weight on the winding crank--have an assistant with you in the clock
room to release the ratchet[s]. Don't try to do it all alone. Too many
things can go wrong.)
|
29 Swaged
(compressed) fittings should always be applied as recommended by the
rope manufacturer. Soldered fittings are always applied to properly
cleaned rope with pure zinc solder or babbit metal. In some instances,
the use of thermo-setting resins is permitted, but the socketting must
be done correctly. Once again, follow the rope manufacturer's
recommendations. His good reputation depends to a great extent on his
good advice.
34
Make sure that the ropes or the winding barrels are clearly marked to
prevent overwinding and the consequent possibility of damage to the
pulleys, the rope and the clock. Paint doesn't work well as a marker on
wire rope--it splits off the strands as the rope runs around the
pulleys. Tape may last a bit longer, but has to be renewed rather
often. It is not a good idea to open (birdcage) the strands to insert a
marker that is woven or interleaved into the strands. Lord Grimthorpe
suggests a positive stop, which has some dangers of its own if the
winder isn't paying attention, or an electrical alarm of some sort to
alert the winder that he is at the end of his rope, so to speak, which
is probably the best idea. Consider the clever soul in New Jersey who
recently took an electric impact wrench up to the clock room, popped the
socket on the winding square, pulled the trigger, and reeled in all of
the weight line, except for the part that broke off and followed the
weight all the way down.
While you are working with the ropes and the weights, always
remember (and think about) where the downward flight path of the weights
will take them should the rope break. It is a good idea to have a
catch box (about 3 ft x 3 ft x 2 ft high) filled with rocks--not sand or
gravel--under the weight to absorb the force if the weight falls; it's
even better if the weight can fall all the way to solid ground. If the
weight channel ends above a normally inhabited area, the floor
directly under the weight should be seriously reinforced (preferably
under the supervision of a professional engineer), a rock-filled catch
box installed, and/or a stop cable attached to the weight--anything that
will prevent shorter people and longer weight chutes. While you're
pondering the flight path of the weights, take a long, hard look at the
pendulum. Many of these particular weights have been swinging on the
same suspension spring for over one hundred years, and that spring might
be on the verge of failure.
35
The worst 'repair' to a suspension spring I've seen yet involved a
section of hacksaw blade--with the teeth still on it--suspended on a
nail. I still have it, and I may frame it. It worked--for a very short
while--but fortunately there was a very solid floor underneath the
pendulum. Most pendulum enclosures I've seen will merely provide a
momentary check to the pendulum, after which the acceleration of gravity
will again take over at 32 feet per second per second. A 100 pound
pendulum falling through 20 feet is capable of delivering a hammer-blow
of 2000 foot-pounds. That's more than enough to punch through the
typical attic floor and the ceiling below, and is guaranteed to ruin
someone's day. A stop pin, or a stop cable attached to the pendulum is
recommended.
Electrical Safety Considerations:
Run, don't walk, away from a clock installation that has electrical
wires sharing the weight channels. That is a fire looking for a place
to happen. If weights are moving up and down the channels, the wires
must be removed, even if the wires are encased in conduit.
The electrical code may allow conduit-enclosed fire or intrusion alarm
wiring (low voltage) in the weight channel in some areas, but it is not a
good idea in any case. Check with a state licensed electrician or a
fire marshall--there's just too much at stake.
An electrically rewound clock should be checked carefully: many
of the potential dangers that are specific to manually wound clocks will
also appear. Remember that most, if not all, of these clocks were
wired long before a National Electrical Code appeared. If the motor
wiring or the switch wiring (or any of the wiring in the clock room),
appears to show signs of obvious age and need of attention, recommend to
the owner of the building that the system be rewired. It pays to be
rather blunt about this, even if you lose a job, particularly if the
clock owner claims the installation is grandfathered.
36
Grandfathering in a case like this is immaterial and irrelevant--an
unsafe electrical system is still an unsafe electrical system--there is
just too much of a possibility that something will go wrong while you
are working on the clock, or during the warranty period. I, for one,
don't want to be responsible for the loss of a building on the National
Historic Register (or any building), much less another tower clock.
These electrically re-wound clocks should also be checked for possible
problems with both pendulum bobs and driving weights. In most cases,
the weights are suspended on chains--some of which have been in use for
over 70 years. A thorough cleaning and a link-by-link examination of
the chain is in order. These chains will
stretch, to the point that they no longer fit the sprocket(s) on which
they ride. You may (probably will) have to get a new sprocket, and
chain. Motorcycle drive chain with a breaking strength of at least 1000
pounds is recommended. Lubricate the chain with a synthetic,
silicone-bearing penetrating lubricant, whether the chain is the
original or a replacement. Reinforcement of the clock room floor may be
called for, or the installation of a catch box or a stop cable for the
weights, depending on the configuration of the weight system. The
action of the rewind start and stop switches should be carefully
checked. Switches on a 70 year old installation may be the originals,
very likely with badly worn contacts, and should probably be replaced.
(Some of these old switches actually used slate as an insulator.) If
the clock dials are illuminated, check the switches which control the
lights; check the switch actuator, and check the electrical wiring.
If there is no fuse-box or circuit-breaker box in the clock room, insist
that one be installed before you do any work on the clock. It is
dangerous (to you, to the electrician replacing a rewind motor, or to
the custodian changing a light bulb) if it is necessary to go all the
way down to the main breaker box, shut off the breaker for the clock,
hang a tag on the breaker, and go back up to the clock room. Building
custodians (particularly in a public building) have a tendency to forget
that someone is working on the clock, and have been known to ignore
warning tags on breakers, simply because the breaker also controlled
another circuit someone else wanted to use. I've seen a church clock
which had evidently been rewired by someone within the church--obviously
someone who was not familiar with (or ignored) Code --that would give
an electrician a seizure. The rewind circuits had been rewired with zip
cord. Zip cord is a 'technical' term for a household extension cord.
Worthy of mention and caution on these electrically re-wound clocks
is the danger associated with the rewind gearing system. These gears
are driven by a high-speed electric motor, and via the gearing down,
exert tremendous torque. Keep your hands away from these rewind gears
while power is applied to the rewind system.
37
Wire Rope Inspection:
OSHA has developed various checks and guidelines which will be,
if they haven't already been, applied to tower clock weight line
systems, and their proper rigging. One of these involves checking the
rope for broken wires by running a shop towel along the cable. Any snag
indicates a broken wire. If you do this check, please don't do it with
your bare hand! Rope replacement is a given if the wire rope on a
crane has any of the following defects (and the same standards should
apply to a clock weight line):
1. 1 (one) valley break. A valley break occurs
at the wire/core interface, and indicates poor or non-existent rope
lubrication, and excessive wear at the wire/core interface of the rope.
Lubrication will not correct the condition.
2. In running ropes, six randomly distributed broken wires in any one
lay, or three broken wires in one strand of one lay. (One lay is that
part of rope in which a specific strand makes one full turn around the
core.):
3. Kinking, crushing, birdcaging, reduction in rope diameter, or any
other damage resulting in distortion of the rope structure:
4. Wear comprising one-third of the outside diameter of outside individual wires:
5. One outer wire that has broken at its contact point with the core
of the rope and protrudes or loops out from the rope body:
which seem to be good guidelines for those working with tower clocks.
Pulleys will be inspected, and the owner of the clock will have to
replace any that are too small in diameter, incorrectly installed, or
otherwise incorrect. Ratchet wheels and pawls on the clock will also be
inspected for excessive wear and free operation. The custodian, or
you as the clockmaker, should inspect the entire weight line on a
regular basis, and that means inspect the entire line, not just that
visible portion that reappears on the barrel every week.
38
Crawling or tight-roping along a ceiling joist into the corner of an
attic whilst wiping a towel along the rope, and simultaneously trying to
avoid falling through the ceiling isn't at the top of anyone's 'To Do'
list on a mid-summer afternoon, but the greatest wear, and the greatest
possibility of damage to the rope is always off in a dirty and
inaccessible corner. Corrosion is an insidious enemy of wire rope. A
wire rope may show little external evidence of damage, yet the inside
may be seriously rusted because it was never lubricated. Do your
inspection on a rainy day, and check the roof for leaks (particularly
over the weights) at the same time. It's good P. R., and will be very
much appreciated by the clock owner.
Clock Room Safety Checks:
You may also want to remind the custodian and the clock owner that
OSHA doesn't like to find bird droppings on and around the clock.
Co-residents such as bats and birds are not welcome in the clock room,
regardless of OSHA--they spread various unwelcome diseases to
clockwinders and clockmakers--their droppings can be very abrasive, and
can react chemically with clock metals. In the Northeast, I've noticed
that cluster flies will crowd into a clock room in the fall, and crawl
all over the clock. Many of them meet their doom in the teeth of the
wheels, to the detriment of the teeth, because insect exoskeletons are
also rather abrasive. Don't try to keep the cluster flies out--it's
impossible--but try to keep the wheel teeth and pinion leaves clean.
Steeples and clock rooms should be sealed to keep larger vermin out, and
any areas used in normal maintenance of the clock should be cleaned up.
If the clock room is not clean, OSHA may well tell the clock owner to
clean it, or shut it down. Bird and bat droppings are a distinct health
hazard to everyone, particularly to the clockmaker who has to work in
an area where he may breathe in or otherwise ingest viral or bacterial
infectors. Psittacosis is no fun whatsoever. The Mercks Veterinary
Manual (5th Ed.) states that "The disease occurs worldwide...Aerosols
and dusts from respiratory discharges and digestive dejecta (pigeon
poop) are infective." A mask is recommended in the work area--it's much
less expensive than treating psittacosis--as are a bath and change of
clothes immediately after leaving the work area.
39
Lubrication:
Lubrication of the wire rope is a necessity. Lubrication will retard
corrosion, and decrease friction and wear by allowing the wires and
strands which make up the rope to slide past one another as they bend
around a pulley or winding barrel. The lubricant prevents
metal-to-metal contact and prevents corrosion. The simplest and
quickest check is to rub a finger in the groove of a pulley. If no
lubricant is apparent, the need for lubrication is immediate. Lord
Grimthorpe recommended a lubricant (to be worked into the strands by
hand!) made up of tar and grease. Somehow, the author has the feeling
that this lubrication method will not find much favor with fastidious
clock custodians, particularly those whose clocks have wood winding
barrels. Some modern wire rope lubricants are nearly solid, and have
to be heated to 160 to 200 degrees F., or thinned with gasoline, before
they are applied to the rope. Needless to say, none of these lubricants
are recommended for use in any steeple or in the clock tower of any
building!
The desired end result in lubricating a wire rope is to get the
lubricant into the core of the rope, that the various wires which make
up the rope can slide past one another as the rope bends over a barrel
or a pulley. A lubricant-impregnated fiber core will help a great deal
in preventing corrosion. Modern recommended lubricants for crane ropes
are a heavy oil or a grease carrying either molybdenum disulphide
(preferred; also known as MOS2) or graphite. It is unfortunate, but
both of these lubricants are very dirty. MOS2 usually has to wear off
if you get it on your hands, and clothes stained with it are stained
forever. Graphite isn't very far behind. If something cleaner is
preferred--and it usually is--the heaviest grade of Mobil 1 (a synthetic
oil) has been recommended for wire ropes. This particular brand of
oil, in a lighter grade, is also used as the lubricant of choice for the
pivots on a tower clock. After extensive reading in the literature, my
conclusion is that the wire rope system for a clock is most similar in
general requirements to that of an elevator.
40
Both are protected from the weather, both require frequent inspections,
and the failure of either system can be rather dangerous. Perhaps the
simplest means of maintaining the proper amount of lubricant on a wire
rope is with a felt pad, wick-type lubricator. Although this method
will not oil those parts of the rope off in a far corner of the attic,
it could be placed so the usually hard-to-reach portions of the rope are
kept oiled. Williamsport Wirerope Works, Inc., recommends a light
viscosity Spindle oil30.
More and more clockmakers who work on tower clocks are using
synthetic motor oils. These oils have very wide temperature ranges, and
don't tend to dry out and gum as rapidly as do mineral oil-based
lubricants.
An industrial spray lubricant carrying MOS2 is available, but evidently
only in 55-gallon drums. If you don't absolutely have to carry
something (a 55 gallon drum!) up to the clock room, leave it below. It
is difficult to make any specific recommendations on oil application
methods, because there are so many different clock weight line
configurations, but the felt pad, wick-type lubricator is probably the
most effective. However messy the lubrication job might turn out to be,
it is necessary to the life of a wire rope. It is also a safety
procedure, and safety is of primary importance in any work with tower
clock weight line systems.
A word of caution. Many of the old tower clocks use winding
barrels made of oak. Oak has a tendency to react chemically with some
mineral oil-based lubricants. Various articles in past issues of the
BULLETIN caution against oiling unbushed pivots in a wooden works clock
for this reason. It is strongly recommended that any wood barrel be
covered with sheet metal to avoid this possible reaction, and to keep
the cable from cutting the surface of the winding barrel.
30 Light
viscosity' is calculated to be a Saybolt Seconds Universal (SSU)
viscosity rating of 34 to 38 seconds at 210 degrees F., which equates
roughly to a 10 weight oil under the more familiar API (SAE) viscosity
ratings.
41
Probable Trouble Spots:
The first check on a weight drive system should start at the clock.
Likely areas of trouble will be:
1. Improper termination of the weight line at the winding barrel.
2. Wrong D/d ratio for the winding barrel diameter/rope size.
3. Improper lay of the rope, i.e., right hand lay attached at the left
side of the barrel (overwound barrel); left hand lay attached at the
right side of the barrel (overwound barrel). The lay and the
connection points are just the opposite with an underwound barrel. Also
wrong type, grade, or rope size.
4. Incorrect fleet angle between the winding barrel and the first, or lead, pulley.
5. Insufficient diameter (D/d ratio) of pulleys in the weight line system.
6. Dirty, improperly lubricated pulleys, or pulleys made of inappropriate materials.
7. Lack of lubrication of the rope and resulting rust.
8. Loose weight hooks and/or improper connections to their pulleys/lines.
9. Inappropriate and unsafe flight paths for the weights, (and the
pendulum) i.e., the floor beneath the weight is inadequately
reinforced, the weight of the pendulum will not be supported by its
enclosure/stop pin/stop cable.
10. Uninspected weight lines (most common if a galvanized or stainless rope has
been installed).
11. Weight line too short, rope terminator may pull out of or off of, winding barrel.
12. Badly worn, or binding ratchets on great wheels/winding barrels.
13. No warning markings on the weight line, or no alarm to warn that weights are
all the way up.
14. Excessive weight after the system has been redesigned with low friction pulleys,
etc.
42
15. Switched weights (the time side is usually the lightest [smallest]).
16. The custodian. This is usually the source of most clock problems.
Historically, most custodians (and clock owners) are ignorant of any
safety precautions; custodians are (usually) grossly underpaid; and
almost invariably totally horologically ignorant. A maintenance guide
and clearly written instructions may help to remove most of this
particular potential trouble area. Emphasize to the clock owner that it
is best that only one person be charged with care of the clock. An
excess of ignorant (however well-meaning) hands have been known to
result in damage to the clock, the building, and to the well-meaning
hands.
Do not construe the above to be the last word in safety
considerations or in design criteria for tower clock weight systems.
There are so many different installation requirements and restrictions
that no one article can possibly cover all situations. I do recommend
that you become familiar with the ANSI and OSHA requirements for the
installation, care and maintenance of wire rope systems, and use a lot
of common sense. Make sure that the clock custodian is aware of what
he has to do to properly care for and maintain the weight drive
systems. I have found it a good (and very much appreciated) practice
to compile a maintenance document which covers oiling and greasing
instructions for the clock and bell strike mechanisms; for the
inspection and care of the weight drive system; inspection of automatic
rewind systems, and precautions for all of the systems used in a
particular installation for the custodian of each tower clock
installation. These instructions are always provided as a part of my
contract in any bid I make on any tower clock. It has been my
experience that word-of-mouth instructions on the care of the clock
become garbled over the years, or are simply not passed on to the new
custodian. The instruction sheet provided by many clock manufacturers
is totally inadequate today, since tower clocks no longer figure so
prominently in our lives, and there is so little in the literature to
which the custodian, or, indeed, the clockmaker, can refer for
assistance.
43
In short, use common sense, ask questions (a local rigging company is
a good source for information--they work with weights and wire ropes
daily in all kinds of weather and are familiar with the requirements and
codes), and ask for help if you don't know the solution to a problem.
The only stupid question is the one you didn't ask.
Oh, the snatchblock? That's a block with one removable
cheekpiece, so the pulley can be located in the middle of a cable
already solidly fastened at both ends. Also known as a gateblock. Very
handy for the poor soul who has to thread a wire rope through all those
pulleys.
THE BITTER END
Acknowledgements:
My special thanks go to Williamsport Wirerope Works, makers of
Bethlehem Wire Rope®, for permission to use their data and illustrations
in this article, thanks to Sam Ledbetter for his advice and suggestions
on cable lubrication, to the Balzer Family for sharing their expertise,
to Frederick M. Shelley for encouragement, and to the local churches
who let me work on their clocks.
Suggested further reading:
ANSI Standards:
ANSI/A11264.1 Stairs and Railings (for information only, but it might be
a good idea to bring this standard to the building owner's attention.)
ANSI/SAE J881-OCT80, Lifting Crane Sheave and Drum Sizes.
ANSI/SAE J959-MAY91, Lifting Crane Wire-Rope Strength Factors.
Combined Federal Regulations (CFR) Chapter XVII, ß 1910.179-.183, ß1926.550-.554
Federal Specification RR - R - 571a; Minimum pulley and rope diameters.
U. S. Simplified Practice Recommendation 198-50. (Maximum rope loading.)
Machinery's Handbook, 24th Edition: Ppg. 323 - 339.
_____________________
44
APPENDIX I:
CABLES BIBLIOGRAPHY
AKED, Charles K., Gravity Drive in Large Clocks: BULLETIN of the NAWCC,
#261, August, 1989
GORDON, G. F. C., Clockmaking Past and Present: The Technical Press, Ltd.,
London. 1928.
GREEN, Robert E., Ed., Machinery's Handbook, 24th Ed.: Industrial Press, Inc.
200 Madison Avenue, New York, NY 10016.1992.
PENMAN, Laurie, M.B.H.I., Clock Design and Construction: ARGUS BOOKS
LTD, Wolsey House, Hemel Hempstead, Herts, England,. 1984.
SHAPIRO, Howard I., P.E. Cranes and Derricks: McGraw-Hill Book Company.
New York. 1980.
SIEGMUND, Otto H., Ed., The Merck Veterinary Manual, 5th Ed.: Published by
MERCK & Co., Rahway, New Jersey. 1979
COMBINED FEDERAL REGULATIONS (Chapter XVII ß 1910.179 -.183, ß1926.550 .554)
of the United States Government. Government Printing Office, Washington, DC. 1994.
WILLIAMSPORT WIREROPE WORKS, INC., Wire Rope Catalogs and Technical Bulletins:
Williamsport Wirerope Works Technical Staff. Privately printed, 1992.
APPENDIX II:
Formulas
|
Should anyone find an error in any of these formulas,
or a lack of clarity as to their intended use, please
.
While I don't have the expertise of the late Donn Haven Lathrop,
I will do my best to resolve your concerns. / CSZ / Nov.2017
|
1. Weight Drop, Compounded:
Cvd = Tvd x (1/F) where:
Cvd is compounded drop, in feet;
Tvd is total weight drop required, in feet;
F is the number of falls.
The reader must be reminded that the sheave(s) take up a finite amount
of space above the weight, a space that must be taken into consideration
in calculating the required weight drop.
2. Mechanical Advantage:
1. The accepted definition of a mechanical advantage is
the ratio of effort to resistance, or, MA = R/E ; however, to compute a
mechanical advantage ratio (really a disadvantage ratio, in that more
weight is required with multiple falls), which is necessary to derive
the total weight required in a compounded weight drive system, a
permutation of the formula is required. Counting the number of falls at
the weight and multiplying the design weight by the number of falls
yields the same result.
R = FE, where:
R is the total weight required, in pounds;
F is the number of falls;
E is the actual weight required to drive the clock, in pounds.
(It must be remembered that this is a simple solution; no allowance is made
for frictional losses and bending loads.)
2. The mechanical advantage of a winding jack, wherein a smaller gear
(pinion) drives a larger gear is;
MA = Dt/Pt, where;
Dt is the number of teeth on the driven gear, and;
Pt is the number of teeth on the driving pinion (gear).
This is only the MA of the winding jack itself: the total mechanical
advantage must also include the length of the winding handle, and the
diameter of the winding barrel.
3. D/d ratio; which is the ratio of the sheave (or winding barrel) pitch diameter
to the diameter of the rope;
D = (X d), where;
X is a manufacturer/federal specification constant for differing sizes
and constructions of wire ropes, and;
d is the diameter of the rope in inches.
Pitch diameter is the pulley tread diameter plus one half the rope diameter.
3A. How does one calculate the D/d ratio?
Add the diameter of the drum barrel to the diameter of the wire rope you
want to use. Then divide by the diameter of the wire rope.
Example: When using 1/2" wire rope on a 10.75" drum barrel.
10.75 + .5 = 11.25. 11.25 divided by .5 = 22.5:1 D/d
ratio. This meets the ANSI/ASME recommendation of 15:1 for pulling and
18:1 for lifting applications.
4. Bending stress: sb = Edw /D, where:
sb is in pounds;
E is the modulus of elasticity of the wire rope,
which varies between 1 x 107,
and 1.4 x 107. 1.2 x 107 (12,000,000)
is a frequently used average value;
dw is the diameter of the component wire
(for 6 x 19 rope, dw is .063d);
D is the pitch diameter of the pulley in inches.
To calculate bending stress; sb, in the outer wire(s), and the bending load;
pb, use these formulas:
sb = Edw /D, for bending stress; and
pb = sbA; where A = d2Q.
E is the modulus of elasticity of the wire rope, which varies between 1 x 107,
and 1.4 x 107 . 1.2 x 107 (12,000,000)
is a frequently used average value.
d is the rope diameter; dw is the diameter of the component wire
(for 6 x 19 rope, dw is .063d);
D is the pitch diameter of the pulley in inches; A is the
metal cross-sectional area of the rope; and Q is a constant derived for a
specific type of rope. For 6 x 19 wire with a fiber core, Q is .405.
5. Bending load; pb = sb A; where A = d2Q;
where:
pb is in pounds;
d is the rope diameter;
A is the metal cross-sectional area of the rope; and
Q is a constant derived for a specific type of rope.
For 6 x 19 wire rope with a fiber core, Q is .405.
N.B. In both 4. and 5. above, constants such as dw,
A, and Q, are provided by the rope manufacturer.
6. Radial pressure on a pulley or a barrel:
P = 2T / (D d) , where:
P is radial pressure in pounds per square inch;
T is rope tension in pounds;
D is tread diameter of barrel or pulley in inches;
d is rope diameter in inches.
7. Calculating weight of solid stone driving weights:
W = (h x d x w x 160) / 1728, where:
W is in pounds, and;
h, d, & w, are in inches;
1728 is cubic inches in a cubic foot;
160 (lbs) is an empirically derived constant (see text).
8. Fleeting pulley/sheave placement;
Fsp = barrel depth/2 x .035, or;
Fsp = barrel depth x 1.25 (ft.), where; Fsp and barrel
depth are in feet.
[Editor's Note: Numbering of these formulas is Donn's original;
"8" was duplicated.]
8. To compute the effort and resistance of a lever, as in a barrel/great wheel:
Lea x R
Lra E
where:
Lea is the length of the effort arm;
Lra is the length of the resistance arm;
R is the resistance (usually in pounds), and;
E is the effort (usually in pounds).
9. To compute frictional losses due to pulleys and wire bending loads:
P = W/r where
P is the force at the winding drum,
W is the weight (in pounds) of the driving weight
r (to compute frictional losses in rewinding the clock [lifting the weight] ) is
r = (1 - µ)m + 1 + (1 - µ)m + 2 +. . .
+ (1 - µ)m + n
where
m is the number of 180° bends the rope makes at the weight;
n is the number of parts of line.
µ is the loss coefficient (friction due to pulley bushing[s]),
expressed as a percentage, e.g., with a 2% friction loss; µ = .02.
r (to compute frictional losses in driving the clock [weight falling] ) is:
r = | ___1____ | + | ___1___ |
+. . . + | ___1___
|
| (1 - µ) m + 1 |
| (1 - µ) m + 2 |
|
(1 - µ) m + n |
An example: Assume a 50 pound weight is needed to drive a clock,
requiring a triple fall (3 part) compound system:
Simple solution, disregarding r (no friction component): 50 x 3 =
150 + 10 (pulley weight) = 160 pounds; therefore 160/3 is 53.333 lbs.
The weight itself must weigh 47.666 pounds.
The complex solution:
Winding the clock: Let µ = .02, m = 1, and n = 3
1 - µ = .98, therefore:
r = .982 + .983 + .984
(this is: .98 squared; plus .98 cubed, and so on.)
therefore:
P = 160 / 2.82 = 56.74 lbs. (effective resistance to rewind effort)
Driving the clock:
r = |
___1____ |
+ |
___1____ |
+. . . + |
___1 ___ |
|
(1 - µ) m + 1 |
|
(1 - µ) m + 2 |
|
(1 - µ) m + n |
or:
r = |
___1___ |
+ |
___1___ |
+ |
___1___ |
= 3.18 |
|
.982 |
|
.983 |
|
.984 |
P = 160 / 3.18 = 50.32 lbs. (effective driving weight required)
These figures are ideal calculations--no real world modifiers
such as a lack of lubrication, loading of the external hands, etc., are
involved in the calculation. Still rather empirical, isn't it? We are,
however, getting close to being able to determine the theoretical
required weight to drive the hypothetical clock. Note, however, that it
does take more effort to rewind a compound weight system.
10. To calculate the maximum length of rope (L) that can be wound on a winding barrel:
L = (A + D) x A x B x K, where:
A = nominal rope diameter,
D = diameter of barrel, inches,
B = width (or depth) of barrel, inches
K = appropriate factor from table below:
Rope Dia. (in) | Factor |
3/32 (.094) | 23.4 |
1/8 (.125) | 13.6 |
3/16 ).1875) | 6.14 |
1/4 (.25) | 3.29 |
5/16 (.3125) | 2.21 |
3/8 (.375) | 1.58 |
7/16 (.4375 | 1.19 |
1/2 (.5) | .925 |
11. To calculate the theoretical maximum length of rope which can be wound on a barrel:
L = (D x pi) x (B/A) — 12, where:
D = barrel diameter, inches
pi = 3.141592654
B = width of barrel, inches,
A = nominal rope diameter
APPENDIX III:
Glossary of wire rope terminology.
ANSI: The American National Standards Institute, from whose
criteria the OSHA standards for safe operation of cranes and derricks
and other systems using wire rope isntallations are derived.
birdcaging: An expansion of the strands laid into a rope;
usually caused by twisting against the lay (q.v.).
block: A system of sheaves (q.v.) sharing a common frame,
and (usually) a common axle.
compounding: A system of sheaves and weight lines
designed to provide a shorter weight drop for (or a mechanical advantage
in lifting or supporting) a weight. The decrease in weight fall is
found by multiplying the total weight fall necessary by the inverse
(1/number of falls) of the number of falls (q.v.). The mechanical
advantage is computed by counting the number of falls going to and from
the moveable sheave(s) attached to the weight.
core: The core material, either metallic or
non-metallic, around which the strands of the rope are helically laid.
Cores are made of fiber (FC), a wire strand (WSC), or an independent
wire rope (IWRC).
Crosby clip: A fastening device, also known as a U-clamp.
A bolt in the shape of a U, used with a forged saddle to terminate a
wire rope, usually in a loop. Strength of a clamped loop is 80% of wire
rope rating.
fall: Any weight line which directly supports the
driving weight. For a single fall, the weight line is attached to the
winding barrel at one end and the weight at the other, without any
compounding pulleys. Compounding requires at least one pulley, and
results in multiple falls at the weight. Two lines at the weight is
two-fall compounding, three lines is three-fall compounding, etc.
Increasing the number of falls increases the compounding advantage, but
also increases losses due to pulley bearing friction.
fiddle block: A block consisting of two pulleys in the same
vertical plane held in place by their common cheek pieces.
Fist clip: A fastening device to be used in creating a
loop in a wire rope. The clip has two forged saddles and two bolts to
pull the saddles together. It doesn't tend to cut into or kink a wire
rope. Strength of a clamped loop is 80% of wire rope rating.
fleet angle: The angle between the sheave/barrel
centerline and the rope at its extreme deflection. The fleet angle
should not be less than 1/2°, and should not exceed 2°.
fleeting pulley: A pivoted guide pulley whose pivot
should be aligned with the centerline of the barrel and placed at a
distance from the barrel determined by this formula: Dw x .5 / .035,
where Dw is the depth (or width) of the barrel; multiplying by .5
takes half of the depth; .35 is a constant derived by trigonometrically
solving for the adjacent by dividing the opposite by the tangent
(.03492) of 2°. The rule of thumb is 1.25 feet of separation between
the barrel and the first, or main, pulley for each inch of barrel depth
or width. The fleeting pulley must not be used as the lead sheave (q.v.)
fleeting sheave: A self-aligning sheave (grooved wheel
or pulley) mounted on a horizontal shaft, which will allow the sheave to
move from side to side as the rope winds on or off the barrel.
See fleeting pulley for location and alignment data.
guard pin: A pin or bolt through the cheek-pieces of a
pulley, so placed as to prevent the wire rope from leaving the groove in
the sheave (q.v.).
lay: (or laid) The lay is the direction of the helical
path in which the strands making up the rope are laid. If the strands
form a helix similar to the threads of a right-hand screw, the lay is
called right, or right-hand; if the strands wind around to the left the
lay is called left, or left-hand. In Lang lay rope the wires in the
strands and the strands spiral in the same direction.
lead sheave: The first, or main sheave, or pulley for
the rope as it comes off the winding barrel. See fleeting pulley for
location and alignment data.
OSHA: Office of Safety and Health Administration. For
information on safety requirements applicable to tower clocks, contact
the local or regional Office.
overwound barrel: A winding barrel system in which the
cable passes over the barrel as it is wound on. A right lay rope on an
overwound barrel should start from the right hand flange, and a left lay
rope from the left flange. See underwound barrel:
plow steel: Plow steels, made in grades ranging through
plow, mild plow, improved plow to extra improved plow, are high-carbon
(.45 to .80%) steels, used primarily in the manufacture of wire ropes.
pulley: The common, or layman's term for a grooved wheel.
See Sheave.
reeving: A term used to describe the path of the wire
rope through a system of blocks. A reeving diagram is a pictorial
rendering of the desired path for the wire rope.
rock weights: Typical weights per cubic foot for various
materials commonly used in tower clock weight systems:
bricks; 125; cement, 137; granite, 168; gravel, 109; limestone, 162;
marble, 168; sandstone, 143; slate, 175; soapstone, 168; sand
(dry), 100.
sheave: A wheel with a grooved rim, mounted in a frame; a
pulley wheel or any similarly grooved wheel, used to guide or change
the direction of the rope or cable.
snag: A broken wire protruding from the body of the rope,
indicating that the rope is probably stressed, either by excessive
weight, or, more commonly, by bending around a sheave whose diameter is
too small.
snatchblock: A block or pulley with one removable or
pivoting cheekpiece, whereby the pulley can be located in the middle of a
cable already solidly fastened at both ends.
soldering: Attaching a terminal to a wire rope with pure molten zinc.
Strength rating is 100% of wire rope rating.
stop cable: A safety device attached to a weight to
prevent its falling beyond the limits imposed by the length (and
strength) of the stop cable.
strand: A wire rope strand is made up of wires;
the strands are then laid (q.v.) into a wire rope.
swage: To fasten a termination to a wire rope by
physically deforming the termination around the rope; as by hammering,
or by hydraulic press. Strength is 100% of wire rope rating.
termination: Any of a number of devices and methods used
to place a working terminal on a wire rope. Swaging (q.v.), soldering
(q.v.), and U-clamps (q.v.) are common fastening methods.
thimble: A grooved metal reinforcement (in a teardrop shape)
placed in a wire rope loop to prevent chafing and cutting.
U-clamp: A fastening device, also known as a Crosby clip.
A bolt in the shape of a U, used with a forged saddle to terminate a
wire rope, usually in a loop. Strength of a clamped loop is 80% of wire
rope rating.
underwound barrel: A winding barrel system in which the
cable passes underneath the barrel as it is wound on. Start a right lay
rope from the left flange, and a left lay rope from the right flange.
See overwound barrel:
Publications:
The catalog of ANSI standards may be ordered from:
The American National Standards Institute
11 West 42nd Street,
New York, New York 10036
Tel: (212) 642-4900
Copies of each of the standards have to be ordered from the catalog,
unless your local library happens to have copies.
|